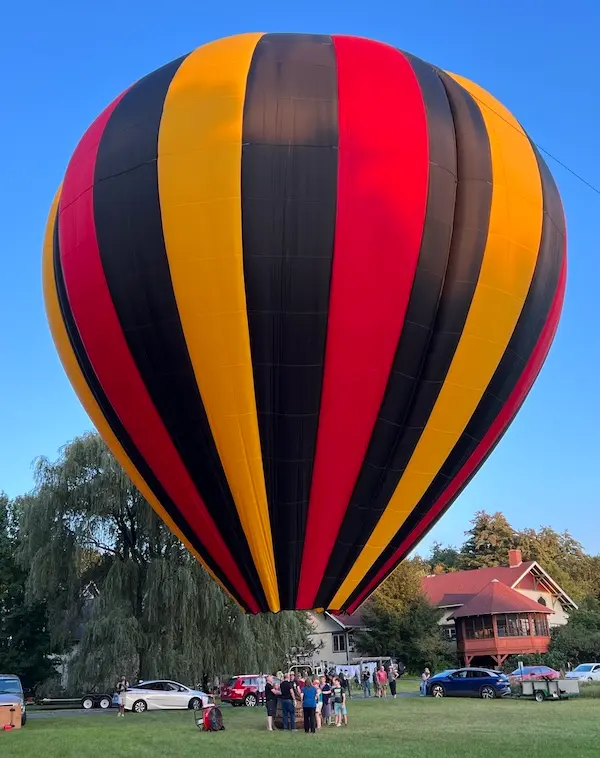
Dan Nachbar's
Motor Balloon Website
TL;DR
I am building a hot air balloon with several propellers driven by small electric motors. The goal of this work is to create a better way to give hot air balloon rides to more people. The balloon envelope is complete and work on the bottom-end is currently underway. My target for starting field tests is Summer of 2024.
Overview
One of my great joys is giving rides in small aircraft. Giving hot air balloon rides is particularly fun.
Hot air balloons typically only fly during the morning and evening hours when atmospheric conditions are most calm. Due to the inherent unpredictability of landing sites, hot air balloon pilots generally don't plan on flying more than one load of passengers on a given morning or afternoon. So flights tend to be about an hour or so long. One-hour rides are nice but suboptimal. Passengers tend to experience diminishing returns after about 15 or 20 minutes. This violates one of the ground rules of show-biz: Leave 'em beggin' for more!
I'd like to give several load of passengers rides on a single morning/evening flying session. The approach I'm trying is to have a balloon that can remain above and/or very near its launch field. With such an aircraft, I could give a sequence of shorter, 15-20 minute rides by staying close to the launch field and repeatedly landing to repeatedly exchange passengers.
The "V1.0" configuration uses four 1-meter diameter (40 inch) propellers driven by electric motors to provide enough thrust to push the balloon around at something like 5 miles per hour. That should be enough airspeed to comfortably remain over or upwind of the launch field in very light winds.
The V1.0 envelope (a.k.a. the big fabric bag) is a custom-built conventionally-shaped hot air balloon. The bottom-end (the structure for the people, fuel, etc.) is built around on a retired type-certified Aerostar wicker basket, burners, fuel tanks, etc. I am adding a battery box at the bottom and a pair of armatures to the left and right sides. Each armature will support two prop/motor units.
Here is a structural schematic drawing of the bottom-end (a.k.a. the basket) of the aircraft -
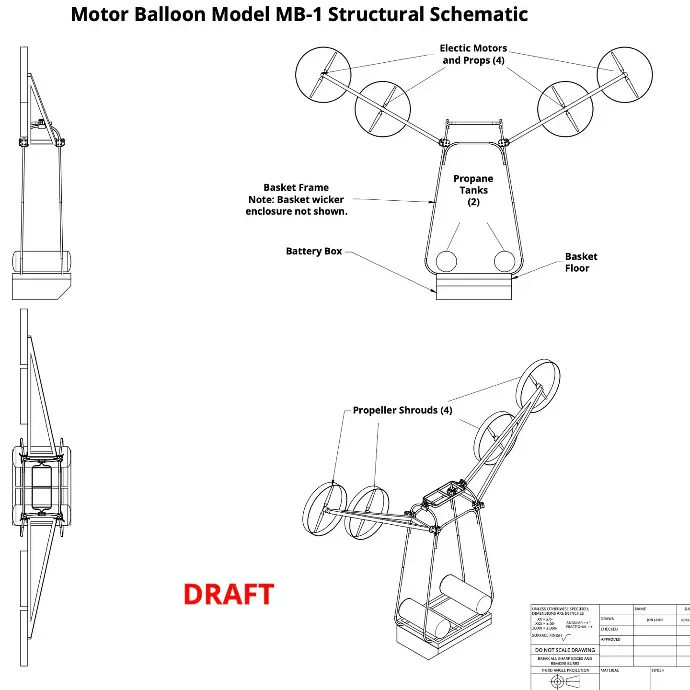
What makes you think you can do this?
I've done something rather like it before - personalblimp.com
What about the Noise?
The motors and props are the same ones used on the quad-copter drones that seem to be effective for some agricultural applications. This approach to generating static thrust works great but commonly a lot of prop noise for efficiency. Having several loud buzzing nasty props will likely ruin the experience for everyone involved.
The most effective way to reduce the noise generated by a prop is to run it more slowly. Those drones are buzzing along at 6,000-7,000 RPM. My plan is to run the props nearer 1,000 RPM. Running the more slowly also reduces the amount of thrust they generate. In order to get enough thrust to be useful, I'll need several large slow-turning props.
The other thing that one can do to reduce noise in the basket is to move the props further away. The "best" place for the props from an aerodynamic point of view is at the equator of the envelope. That's structurally tricky. So I'm leaving that as an improvement down the road.
Construction Status
With a lot of help from friends, I have a fully-built 140,000 cubic foot, conventionally shaped hot air balloon envelope. The envelope had an initial inflation in September of 2023. That inflation test is shown in the photo at the top of this page.
I've been focused on making prototypes for each of the four unique components: the suspension system to support the added weight of the batteries, the battery box located below the basket, the arms on which the motors are mounted, and the shrouds around the props. My target to start flight tests is Fall of 2024.
Presentation Slides
I am presenting an overview of this project at the EAA's Airventure in Oshkosh on Tuesday July 23 at 2:30 PM.
The slides for the presentation can be found here.
Photos from the Shop
Here are some photos of those prototypes in progress -
Battery box in the closed position.
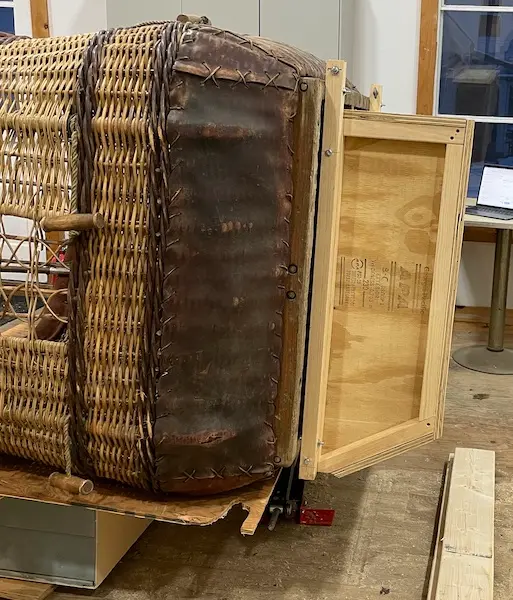
Battery box in the open position.
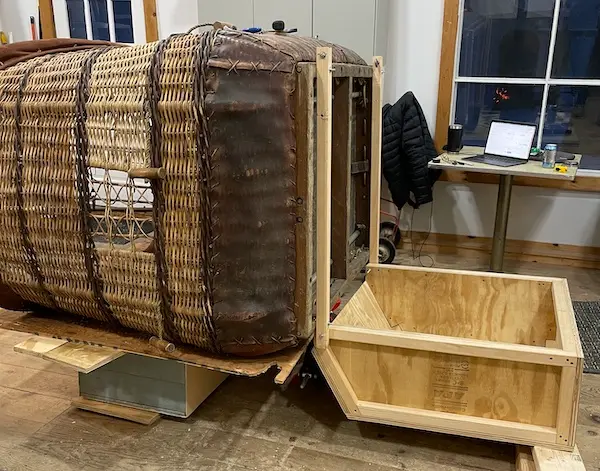
Motor support arm. This also shows the basket in the inflation position. A bevel on the bottom side of the battery box help keep the heavy basket tipped up a bit to make inflation easier for the pilot.
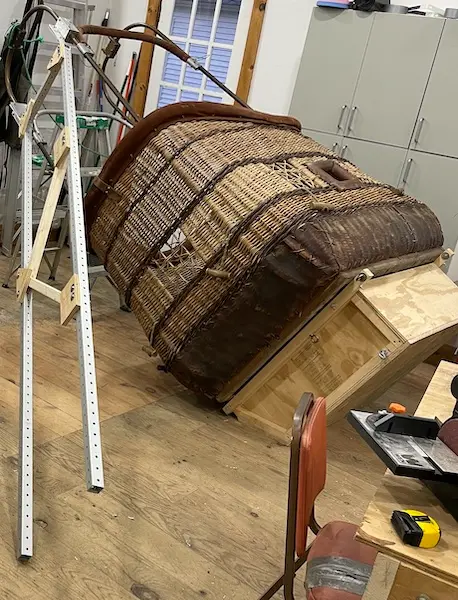
One of shrouds (rings) that will go around the props. The shrouds will provide separation between the scary sharp spinning things and the people - both in the basket and on the ground. I suspect that they will also help reduce prop noise in the basket.
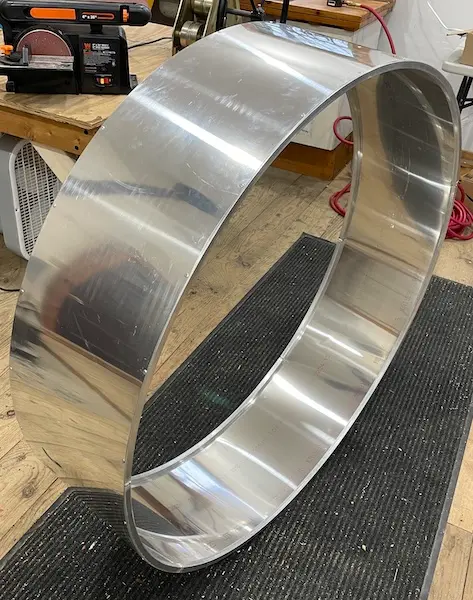
A view of the suspension system geometry. The suspension lines from the envelope will attach to a aluminum blocks added near the top of the pre-existing support posts and lines will run from those blocks to the battery box attached below the pre-existing basket.
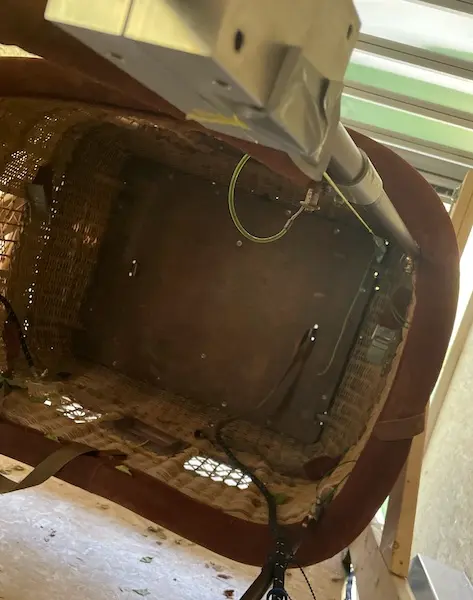